Molding the Future: An Inside Look at Injection Molding
Welcome to the world of injection molding, where precision meets production to shape tomorrow's innovations. At the heart of this manufacturing process are the skilled artisans known as injection molders. These professionals wield expertise in transforming raw materials into intricate designs that drive industries forward. Through a blend of technical mastery and creative vision, injection molders play a vital role in shaping the future of various sectors, from automotive to healthcare. Let's delve deeper into the realm of injection molding and unravel the artistry behind these unsung heroes of modern manufacturing.
History of Injection Molding
Injection molding has a rich history dating back to the late 19th century when it was first developed as a method to produce simple items like buttons and hair combs. Over time, advancements in technology and materials enabled the process to be used for a wider range of products, revolutionizing manufacturing across industries.
The first plastic injection molding machine was patented in the 1920s, opening up new possibilities for mass production of plastic parts. This innovation laid the foundation for the modern injection molding industry, allowing for faster and more cost-effective manufacturing compared to traditional methods.
Since its inception, injection molding has evolved significantly, incorporating computer-aided design and sophisticated machinery to enhance precision and efficiency. Today, injection molder s play a crucial role in producing a diverse array of products, from automotive components to medical devices, shaping the future of manufacturing.
Modern Techniques and Technologies
In the fast-evolving field of injection molding, modern techniques and technologies play a crucial role in shaping the future of manufacturing. One notable advancement is the use of computer-aided design (CAD) software, which allows for precise and complex mold designs to be created with ease. This has revolutionized the efficiency and accuracy of the injection molding process.
Additionally, the integration of automation and robotics has greatly improved the speed and consistency of production in injection molding facilities. Robots are now commonly used for tasks such as part removal, quality inspection, and packaging, reducing the reliance on manual labor and increasing overall productivity. These advancements have helped manufacturers meet the growing demand for high-quality molded products.
Furthermore, the adoption of sustainable practices in injection molding has gained momentum in recent years. From utilizing biodegradable materials to implementing energy-efficient machinery, the industry is making strides towards reducing its environmental footprint. This focus on sustainability not only benefits the planet but also enhances the reputation of injection molding as a forward-thinking and responsible manufacturing method.
Applications in Various Industries
Injection molders play a vital role in the automotive industry, producing a wide range of components such as dashboards, bumpers, and door panels. These precision-engineered parts are highly durable and resistant to wear, making them essential for maintaining the safety and functionality of vehicles on the road.
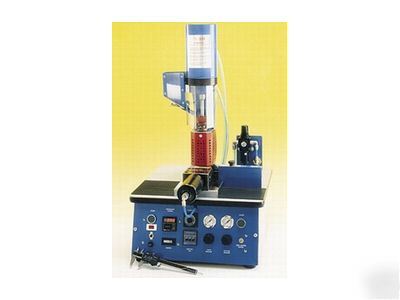
In the medical field, injection molding is utilized to manufacture intricate devices and equipment like syringes, IV components, and surgical instruments. The ability to create custom-designed parts with tight tolerances ensures that medical professionals can rely on these products for accurate and consistent performance in critical healthcare settings.
The consumer electronics sector benefits greatly from injection molding technology, using it to produce sleek and lightweight parts for smartphones, laptops, and other electronic gadgets. By leveraging the versatility of injection molders, manufacturers can meet the demand for high-quality products that are both aesthetically pleasing and functionally efficient.